1. Requirements
More>>Reference Files>>Repair & Maintenance>>Requirements
Requirements are the individual tasks that must be completed to finish a job.
They may be added to a job individually or via a Service Kit.
•When included in a Service Kit as part of a Service Regime, the requirements are added to the job automatically when the service job is activated
•Requirements can be simple ("Carry out service") or detailed (each individual task is itemised) depending on your needs
•Each Requirement need only be created once and added to different Kits
1.1 Adding Requirements
After creating a requirement, you can enter different flat/estimated times to complete the requirement for different make/models.
E.g. an oil change may take longer on one vehicle than another.
While this level of detail may be useful, it is time consuming to set up and entering a standard flat rate time against the Kit is more usual.
2. Parts
More>>Reference Files>>Repair & Maintenance>>Parts
Not required or available if AusFleet Inventory module is used
See also: Inventory module if you manage stock levels, pricing, stock takes etc. in AusFleet
•Parts can be used to create Kits or added to jobs individually
•When included in a Kit as part of a service regime, the parts are added to the job automatically when the job is activated
•For simple record keeping, generic parts such as "Air Filter, "Oil Filter" "Brakes Pads" etc may be sufficient
•For more detailed recording, specific part codes may be required for different manufacturers/fleet items
•Supplier details may be added for each part if required
.png)
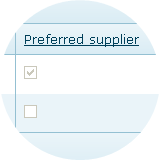
|
You may enter multiple suppliers for each part but only one can be selected as the preferred supplier.
The preferred supplier will default when the part is used but can be changed to alternative suppliers
|
2.1 MMSB Parts
More>>Reference Files>>Repair & Maintenance>>MMSB Parts
Once parts have been entered, they can be allocated to different makes/models.
This then filters the parts list in jobs to display only those allocated to the make/model in the job.
This is optional and can be time consuming to set up but may result in easier ongoing use
3. Kits
More>>Reference Files>>Repair & Maintenance>>Kits
See also: Understanding Scheduled Services
3.1 What are Kits?
Kits contain a list of Parts and Requirements used in services.
They may be built from individual requirements and parts or from another Kit E.g. Kit A = (Kit B) + several individual requirements and parts
•Kits can also contain fixed rate time and costs which provide actual vs flat rate reporting.
By creating Kits and service regimes, service jobs can be scheduled and automatically created with parts and requirements attached, saving data entry time and improving accuracy
Alternatively, Parts and Requirements can be added to each job manually but this can end up taking longer over time.
Kits are important if you:
•Operate an internal workshop
•Intend to schedule services and create jobs automatically
•Wish to minimise day-to-day data entry
•Need a full record of work carried out on your fleet
3.2 Before creating Kits, consider:
1. Are there standard components (parts/requirements) that are used in many Kits I will be creating? E.g. protective covers, standard checks?
If so, create these first so you can add them to other Kits and avoid adding the parts/requirements one by one to every Kit
Example:
•Create "Global Light Fleet Kit" containing "Seat cover", "Wear PPE", "Carry our visual condition inspection", "Check operation of all lights" to add to all vehicle-specific Kits.
•You can only add one Kit to another Kit
2. What level of detail do I need in Kits?
More detail requires more set up but the benefits are better accuracy and audit trail
•A simple "Service as per manufacturers handbook" can be applied to many different vehicles but lacks detail
•A specific listing of all parts/requirements for each Make/Model/Series gives excellent detail and full audit capability but takes time to build
3. How diverse is my fleet?
•A diverse fleet with plant, passenger vehicles and specialised equipment is likely to need a wider variety of Kits than a fleet with only cars.
•Within a light fleet, do you need a different Kit for each make/Model, or are you happy to use a standard Kit for different makes and models
When you know your needs, you are ready to start creating Kits.
3.3 Create Kits
1. Add and name the Kit E.g. Ford Focus A service
2. Add Optional Details
3. Select an existing Kit to copy, if required.
This must be done before adding additional parts/requirements and only one Kit can be imported.
4. Add Parts
Parts need to be added to Parts reference file or Inventory module first
5. Add Requirements
Requirement reference file must be completed first.
4. Regimes
More>>Reference Files>>Repair & Maintenance>>Service Regimes
See also: Understanding Scheduled Services
Service regimes are essential for service scheduling.
If the regime is for Programmed Services tick the "Programmed Service" flag next to the Regime description.
4.1 Schedules Service Regimes
Regimes represent the OEM service schedule by linking a series of Kits (containing parts and requirements) by time and/or utilisation intervals.
1. Add and Name the Regime
Preferably in way that helps identification and is connected with the associated asset(s) E.g. Light Fleet Generic 10000 km/6 months, Volvo Front End Loader, Arrow Kerb and Gutter Layer,
Examples:
.png)
2. Enter Service Intervals
3. Enter Kits.
This example has 4 service types (plus warranty). Each has a different Kit of parts/requirements.
If services have identical parts and requirements, the same Kit can be used for different services.
4. Choose the Makes, Models and Series to which the Regime applies
End of Chapter
|